Modular construction: Using Lego-like blocks to build structures of the future
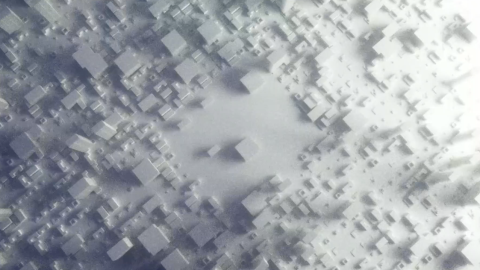
Freethink
- Modular construction involves building the components of a habitable structure in a factory, and then assembling those components on-site.
- The history of modular construction stretches back centuries, and it became briefly popular in the U.S. after World War II, but it’s never quite caught on.
- Construction firms like iMod Structures, which constructs buildings that can be modified and relocated, may soon change that.
Modular construction is on the rise. Once a marginal sector focused on building affordable homes, modular construction is now building an increasing share of structures used for commerce, healthcare, and education. By 2028, the modular construction market is projected to be worth $114 billion.
What is modular construction? It’s like building with Legos but on an industrial scale: standardized block-shaped modules are constructed in a factory, transported to a building site, and assembled together to form a habitable structure.
What’s most striking about modular buildings isn’t appearance but the speed of construction. In 2015, for example, a Chinese construction company built a 57-story glass-and-concrete skyscraper made of 2,736 rectangular modules in a record-breaking 19 days. That’s three stories per day.
In addition to speed, modular construction promises to be more modifiable, more transportable, and less wasteful than traditional construction methods. The method could transform construction, which, despite being one of the world’s biggest sectors, is one of the slowest growing in terms of labor productivity and digitization.
One modular construction firm aiming to bring the sector into the 21st century is iMod Structures, which builds shipping container-sized modules that can be assembled into buildings. The modules can then be disassembled to modify the existing structure or transported to a different site to build a new one.
Freethink recently visited iMod Structures to get an up-close look at its unique spin on modular construction.
Do buildings have to be permanent? | Hard Reset by Freethinkwww.youtube.comTechniques like this could help bring construction into the 21st century. But despite its futuristic and transformative appeal, modular construction is far from a new idea. In fact, the history of prefabrication — the broader category of construction to which modular belongs — goes back centuries.
Prefabrication: From 17th-century cottages to diners to skyscrapers
One of the earliest examples of prefabrication came in 1624, when a colonial American fisherman commissioned an English construction company to fabricate components of a building and ship them overseas to the fishing village of Cap Anne.
In the 17th and 18th centuries, English firms also shipped prefabricated structures — storehouses, cottages, and hospitals — to Australia, South Africa, and New Zealand. In the U.S., prefabricated homes became popular during the Gold Rush when California towns had too many people but too few houses.
In the early 20th century, mass-production made modular construction more practical and, sometimes, more popular. From 1908 to 1940, Sears sold about 70,000 kit homes across the country; some of the cheapest models started around $160. (Kit homes were like IKEA products: the manufacturer builds and precuts the parts, and the buyer assembles them.)
Still, prefabricated homes weren’t particularly popular in the first half of the 20th century; homebuyers generally viewed the structures — especially the metal and experimental ones — as strange and undesirable.
But appearance wasn’t a major concern during World War II. Facing huge demand for cheap and simple housing for soldiers in the early 1940s, the U.S. produced hundreds of thousands of Quonset huts — prefabricated, semi-cylindrical structures made of corrugated galvanized steel — which about six unskilled laborers could construct in a day.
After the war, millions of U.S. soldiers returned home, and the nation faced a housing shortage crisis. Hundreds of companies entered the prefabricated housing market, with several receiving support from the federal government. One of the most iconic models was the enameled-steel Lustron house, which cost $7,000 to $10,000, took two weeks to assemble, and promised to “defy weather, wear, and time.”
By 1958, roughly 10 percent of all homes in the U.S. were prefabricated. In addition to homes, the prefabrication industry also built thousands of diners throughout the 20th century, especially after World War II when owning a prefabricated diner was a decent small-business opportunity. Popular in New Jersey, the narrow diners could easily be shipped to buyers by rail.
Despite the post-war boom, modular construction never really caught on in most parts of the world, though many architects and builders have long been attracted to the method. Some of the reasons include consumer perception that modular homes are unattractive, technological constraints, and the high costs of researching and developing new building techniques.
These challenges can be prohibitive, especially for large-scale projects.
“Building anything over 10 stories in modular is something no one has wanted to do because you have to invest in research and development,” Susi Yu, executive vice president of residential development for the Forest City Ratner Corporation, told Fast Company. “There’s science behind it that you need to figure out.”
But attitudes on modular buildings may be shifting.
“Today, modular construction is experiencing a new wave of attention and investment, and several factors suggest it may have renewed staying power,” noted a 2019 report from the consulting firm McKinsey & Company. “The maturing of digital tools has radically changed the modular-construction proposition — for instance, by facilitating the design of modules and optimizing delivery logistics. Consumer perceptions of prefab housing are beginning to change, particularly as new, more varied material choices improve the visual appeal of prefab buildings.”
The report goes on: “Perhaps most important, we see a change in mind-set among construction-sector CEOs, as many leaders see technology-based disruptors entering the scene — and realizing it may be time to reposition themselves.”
In recent decades, construction firms around the world have built all kinds of modular buildings, including modular skyscrapers in the U.K., U.S., and China; containerized homes in Mexico; and classrooms in rural South Africa.
“In many countries, modular construction is still very much an outlier,” McKinsey noted. “But there are strong signs of what could be a genuine broad-scale disruption in the making. It is already drawing in new competitors — and it will most likely create new winners and losers across the entire construction ecosystem.”
The benefits of modular construction
Modular construction has the potential to deliver $22 billion in annual savings to U.S. and European markets, mainly because of the inherent benefits of building components in a controlled factory setting. The Modular Building Institute lists a few examples:
- Shorter construction schedule. Because construction of modular buildings can occur simultaneously with the site and foundation work, projects can be completed 30 percent to 50 percent sooner than traditional construction.
- Elimination of weather delays. 60 to 90 percent of the construction is completed inside a factory, which mitigates the risk of weather delays. Buildings are occupied sooner, creating a faster return on investment.
- Improved air quality. Because the modular structure is substantially completed in a factory controlled setting using dry materials, there’s virtually no potential for high levels of moisture (which can cause mold growth) to get trapped in the new construction.
- Less material waste. When building in a factory, waste is eliminated by recycling materials, controlling inventory, and protecting building materials.
- Safer construction. The indoor construction environment reduces the risks of accidents and related liabilities for workers.
But perhaps the biggest benefit of modular construction is relocatability and modifiability.
Future-proofing buildings and cities
Buildings are hard to modify and practically impossible to move. That’s a problem for many organizations, including the Los Angeles Unified School District. The district currently maintains thousands of decades-old trailers it built to accommodate a fast-growing student population.
Seeking to replace those trailers with structures, the district partnered with iMod Structures to build “future proof” modular classrooms that can be reconfigured and relocated, depending on fluctuating enrollment levels.
“If you have one of our classrooms in a particular location and 5, 10, or 20 years later, you need them across town at another campus within the school district, you simply disassemble, relocate, and reassemble them where they are needed,” Craig Severance, Principal with iMod Structures, said in a statement. “And it can be done within a few days, minimizing school [downtime] and disruption of our children’s education.”
Founded in 2009 by former real estate investors John Diserens and Craig Severance, iMod Structures takes a hyper-efficient approach to modular construction. Instead of making many types of prefabricated components, the firm makes only one standardized block-shaped frame, each roughly the size of a shipping container. The firm builds the frames in factories and then outfits them with walls, windows, and other custom features the client wants.
Because the frames have the dimensions of a standard shipping container, they can be easily transported to the building site by truck or rail. On site, the frames are connected together or stacked on top of each other. Once the structure is intact, workers finish the job by adding plumbing, electricity, and other final touches.
The process saves a lot of time.
“Typically, it would take nine to 15 months to manufacture a classroom out in the field,” said Mike McKibbin, the head of operations for iMod. “We’re doing that in twelve days.”
Movable neighborhoods
Today, iMod Structures is focusing on future-proofing classrooms in California. But it’s not hard to imagine how this kind of modular construction could transform not only the ways we build buildings but also organize cities. For example, if a company wants to set up offices in a new part of town, it could build an office park out of iMod Structures frames.
But what if the company needs to expand? It could attach more modules to its existing structure. If it needs to shut down? Instead of demolishing the office park, the structure could be modified and converted into, say, a hospital or apartment building. Alternatively, the modules could be removed from the site, and reused elsewhere, so the city could construct a park.
Under this kind of framework, cities could become far more flexible and dynamic, able to quickly adapt to changing needs. And with no need to demolish buildings, modular construction could prove far more sustainable than any method the industry uses today.
“We don’t want our buildings to ever end up in a landfill. Ever,” said Reed Walker, head of production and design at iMod Structures. “We want to take that system and use it again and again and again.”