How can we produce electronics sustainably? Extract rare-earth elements from waste
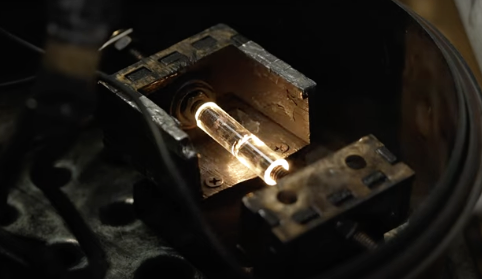
- Producing electronic products like computers and smartphones requires large amounts of rare-earth elements.
- Mining for rare-earth elements is a process that’s costly and often harmful to the environment.
- A team of researchers from Houston’s Rice University recently developed a method that extracts rare-earth elements from existing industrial waste.
A new rapid heating technique can extract rare-earth elements from both industrial and electronic waste. The technique provides a far more sustainable alternative to existing extraction methods, and could be a key step toward the goal of a circular economy.
Rare-earth elements (REEs) including yttrium, europium, and neodymium are key components of modern electronics, vehicles, and clean-energy technologies. Despite their name, these elements aren’t especially uncommon. But unlike other valuable materials found in mineable ores, they tend to be sparsely distributed across expansive regions within the Earth’s crust.
To extract these elements with high enough yields to be economically viable, producers must first leach the ground with concentrated acidic chemicals, convert them into dissolvable salts, and flush them out of the ground using a solvent.
This method is not only both resource- and pollution-intensive, but also can extract dangerous amounts of radioactive elements, which are similarly distributed throughout the crust. As a result, this process has a heavy ecological footprint. By 2015, costs racked up by environmental degradation from REE extraction reached some $14.8 billion in the U.S. alone.
As easily accessible REEs become increasingly scarce within the crust, there’s a rapidly growing need to extract them in more sustainable ways.
Elements waiting in waste
Earth’s crust isn’t the only place where REEs can be found. Each year, vast amounts of industrial waste are produced in which the elements are abundant. These materials include fly ash produced by coal power plants, and bauxite residue (or “red mud”), which is a toxic byproduct of aluminum production.
In addition, REEs are contained in the immense quantities of old consumer electronics we throw out each year, most of which just sit in landfills for decades as they decay. Unfortunately, compared with REEs in the ground, the elements in this waste can’t be extracted quite as easily by converting them into salts. In coal fly ash, for example, they exist as phosphates and glasses, which are far harder to dissolve.
Bing Deng and colleagues at Houston’s Rice University now suggest that these REEs could be extracted easily and sustainably through a technique named ‘flash Joule heating’ (FJH).
Previously, Deng’s team used FJH to convert plastic and rubber waste into graphene: the atom-thick sheets of carbon that are currently undergoing a revolution across various fields in research and technology. In a new study published in Science Advances, they showed how their method could be just as easily applied to REE extraction from industrial and electronic waste.
FJH is an ultrafast electrothermal process where materials are first slightly compressed inside a quartz tube and then loaded between two graphite electrodes — themselves connected to a bank of charged capacitors. As the capacitors discharge, a high voltage is rapidly generated between the electrodes, heating materials in the tube to some 3,000°C in just one second.
In their experiment, Deng’s team loaded the quartz tube with a mixture of coal fly ash and electrically conductive carbon black, which was produced by the burning of petroleum products like gasoline and diesel.
When rapidly heated in this way, the researchers found that REE phosphates and glasses in the ash quickly decomposed to form highly soluble REE oxides, which could then be flushed out by a solvent.
In the most common types of fly ash, the REE yields extracted by the process were more than 200% higher than what would be possible through leaching the waste with concentrated acids.
Also encouraging was the team’s findings that this strategy could be similarly effective when treating bauxite residue or electronic waste. For the five types of REE most critically required by modern clean-energy devices, FJH could produce yields between two and three times higher than some of the most concentrated REE ores found on Earth.
Toward a circular economy
Perhaps the most important test of the technique’s feasibility is its economic potential. In this area, the team’s results are already encouraging. Through their calculations, they showed that the scalability, energy efficiency, and low electricity consumption of the rapid FPH process could enable producers to sell products for over 10 times what they paid for the waste.
Deng and colleagues now hope their method can be rapidly scaled up in the near future. If successful, their efforts could be an important step toward a circular economy — where instead of extracting resources from the Earth irreversibly, materials are gathered by recycling existing waste products. By using these sustainably-sourced REEs in next-generation technologies, the ability of our society to coexist with nature could drastically improve.